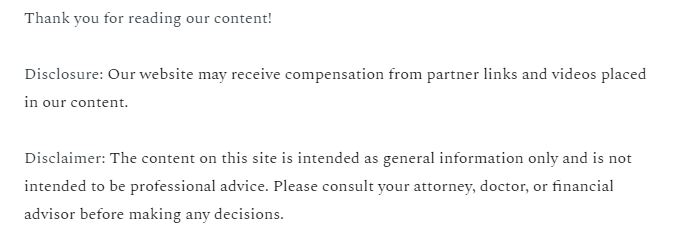

Compressed-air systems are used in a variety of industries. Roughly 70% of all manufacturers, for example, utilize this type of system for a variety of purposes. In order to ensure that these necessary systems are in optimal working order, it’s important to have regular inspections and attend to adjustments, repairs, and other maintenance needs as soon as possible so as not to interfere with daily business operations.
Compressed-Air System Leaks
When a compressed-air system experiences a leak, it can impact a business’ productivity, energy, and financial costs. For example, when a 1/8 inch hole occurs in a 100 pound per square inch system, this can cost a company $1,200.00 a year in wasted energy. Rather than postpone maintenance, it’s important to take care of any sized leaks as soon as possible.
Issues with Pressure Loss
When systems are properly designed, there will usually be less pressure loss. This tends to be less than 10% of the discharge pressure. In order to determine the amount of pressure that is being lost, this figure will be located on the gauge, which is on the compressor’s outlet.
If it’s determined that the pressure loss is more than 10%, it’s important to evaluate the distribution system. When conducting this evaluation, the areas causing these excessive pressure drops can be identified. It’s important to know that when the pressure decreases, every 2 pounds per square inch can reduce operating costs by 1.5%.
Compressed-Air Systems Without Air Receiver Tanks
When compressed-air systems don’t have an air receiver tank, it’s important to add one. This can buffer the short-term demand changes as well as reduce the compressor’s on-and-off cycling.
When determining the size of tank that will be needed, it should be sized to the compressor’s power. Basically, this would mean that a 50 horsepower air compressor would usually require an air receiver tank that is approximately 50-gallons.
Energy Intake and Heat Recovery Units
When an air compressor is being operated, approximately 80% to 90% of the electrical energy that is being used is converted to heat. When these systems have a well-designed heat recovery unit, 50% to 90% of this heat can be utilized for heating the air as well as water.
Energy Intake and Cool Air
When an air compressor is taking in cooler air, these machines use less energy to create the pressure required. If, for example, a 90 degree Fahrenheit intake of air is tempered with another source of cooler air at 70 degrees Fahrenheit, then a 20 degree Fahrenheit drop in energy will occur. This can also lower operating costs by nearly 3.8%.
Clamps for Air-Compression Systems
There are different types of clamps that are used for these systems. Cushion clamps and strut cushion clamps are common to assist with compressed air fittings and distribution.
Energy Conservation Opportunities
According to the United States’ Department of Energy’s audits, there are low-cost energy conservation opportunities available for both small to medium-sized facilities. More than 50% of these facilities with compressed air systems could benefit from these low-cost energy conservation opportunities. In order to find out more about these opportunities, a company can contact this department directly.