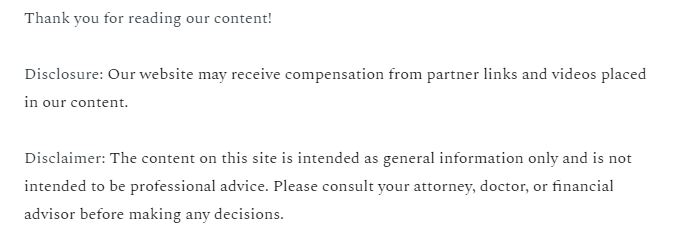
Whether you’re a seasoned expert, or you’re just starting out on your machining journey, learning about CNC workholding is important for every kind of machinist. The machining process can be difficult, confusing, and demanding, but with the right tools and the right mindset, you can dramatically increase your skills and your workflow. Understanding some of the very basic concepts of CNC workholding can prevent you from making mistakes that could end up costing you valuable time and money. With our simple guide, we hope to help get you started on your way to improve and enhance your machining. Let’s begin.
When it comes to machine shop supplies, it’s wise to vary your setup depending on the nature of the job you’re planning to perform. A heavy duty job that takes multiple hours will require quite a more rigorous CNC workholding setup than a job that only needs minimal time and effort. Adjust accordingly to ensure that you are safe and that your tools are able to perform to the highest of their ability. Knowing your workspace and your workholding options is a crucial skill here.
Once you’ve determined the scale and demands of your project, you can begin to determine what type of CNC workholding is appropriate. In the most simple terms, CNC workholding is defined as a tool or device that secures an object to withstand the machining process. Because machining can be quite forceful, the strength of your CNC workholding should never be overlooked. Basic clamps can be used for simple jobs, but more complex jobs require vises, clamps, or devices that can endure a heavier, more trying workload. Some workholding parts may even need to be custom built to ensure a proper hold. For custom parts, it’s smart to deal with trusted industry experts that can assess your needs and cater options based on your particular job.
Preparing to machine is a very important part of the process. You do not want to miss any detail here, as it can end up costing you valuable time, money, and effort later on in the process. By keeping yourself informed and aware, you can act diligently and avoid any unnecessary stress and complications. Before you can begin machining a part, one of the first things you have to do is to tell the machine where part zero is. Part Zero is the datum corresponding to the 0, 0 coordinate on the CAD drawing that you used for all your CAM work, or to generate the g-code for your part program. The right CNC workholding secures your part so you can work with safety and accuracy. This is a crucial piece of setting up your workflow before you get to your tap extractors, end mills, or carbide grinders.
As you continue to prepare your workholding, you should also consider your jigs. Jigs are used to position and secure your workpiece according to your job, then guide the tool to make proper cuts and motions for the duration of the task. These parts are usually custom made for the machining job and can be altered to match movements of the tool as well as the piece you’re working on. By using the right combination of clamps, vises, and jigs, you can secure your job with the confidence you need to move on to other tasks.
Supports are an important part of CNC workholding setups. Generally, supports are placed underneath the workpiece to provide added security throughout the job. Depending on the piece, supports may be placed on the sides for extra stability and to make adjustments more smoothly. All aspects of your workpiece should be considered before you decide on any supports.
Finally, there are some basic concepts related to workholding to keep in mind as you begin your machining work. Tolerance, or the tightness of your clamps, should always be sufficient to provide a certain hold throughout your job. The locations of your workholding can make all the difference, too. Working with a trusted CNC workholding dealer will ensure you get the right parts for the job, every time. Contact us today!